Every now and then, setting up for landing on a wet, short runway, I hear that we should consider the grooved runway to be dry. Is that true?
— James Albright
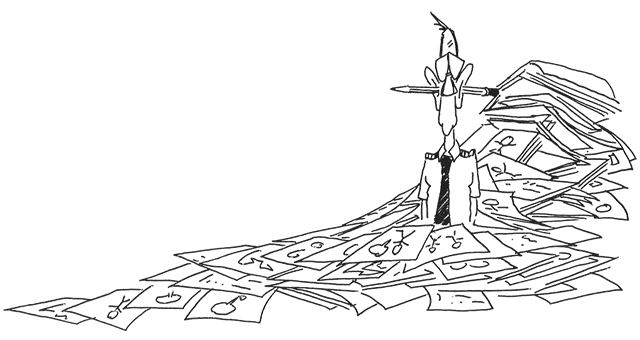
Updated:
2020-04-04
I have flown aircraft that allow this, but the Gulfstream does not in the case of the GVII and most of their "traditional" aircraft. (They do on the G150.) In the case of the GVII, the AFM says "grooved, hard-surfaced runways are approved," but no mention of any kind of performance benefit is made. There isn't a lot of current research out there, most of it was done forty years ago. Aircraft manufacturers can take advantage of grooved runways in performance numbers if they wish, but they don't have to.
We all know intuitively that a grooved runway makes it easier to stop. But braking on a wet, grooved runway as easy as on a dry runway? No, but it is more complicated than that:
- Landing distances on a wet, grooved runway are remarkably reduced almost to the point of being dry, until the water depth is greater than 0.1 inch or if there is any slush. At that point the distances are improved but not nearly as much.
- Balanced field lengths are "essentially dry" for grooved runways in a "wet and puddled" condition. If the runway is slush covered, the advantages of runway grooves are only "slight."
Given that, I wonder if my previous aircraft manufacturer was giving us too much leeway to consider a wet, grooved runway to be dry for takeoff and landing. The key takeaway: if the grooved runway is wet with less than 0.1" depth, your takeoff performance is nearly as if the runway was dry. Your landing distance is improved, but not as dramatically. You still need to plan according to the manufacturer's performance charts, but know you may do better in actual practice.
1 — Grooved vs. porous friction course
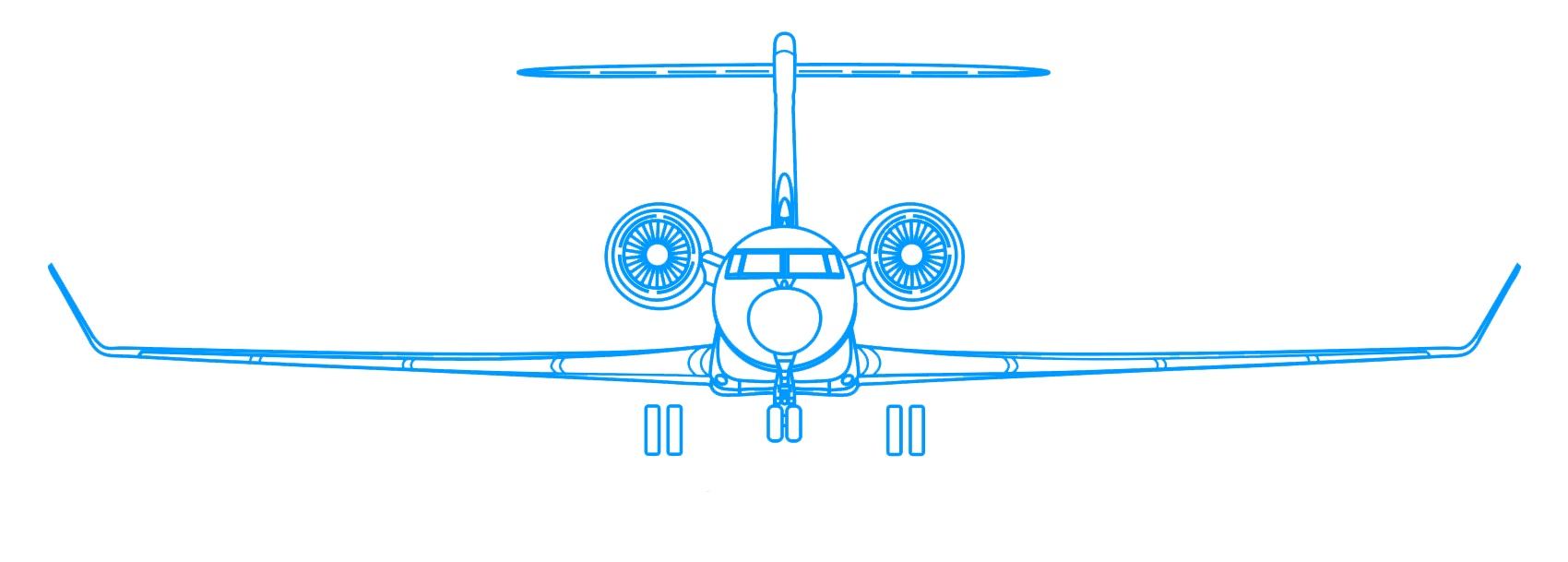
1
Grooved vs. porous friction course
Pavement Surface Modification. Surface texture and surface treatment modifications by themselves will not increase the coefficient of friction of ice formed on the surface, but both will enhance the response of chemical treatment.
- Pavement Grooving. Grooves cut into the pavement will trap anti-icing/deicing chemicals, reduce loss, and prolong their actions. Grooves also assist in draining melt water and preventing refreezing. There is empirical evidence that grooves and porous friction courses modify the thermal characteristics of a pavement surface, probably by reducing the radiant heat loss, and delay the formation of ice. There do not appear to be any negative effects from grooving pavements.
- Porous Friction Course (PFC). PFC has generally the same benefits as grooving. Open graded asphalt concrete is less effective in improving coefficient of friction under icing conditions because the open spaces will fill with compacted snow and, to a lesser extent, with ice in the case of freezing rain. Most maintenance personnel have found that chemical treatment rates may need to be increased on this type of pavement compared to dense graded asphalt concrete because of drainage of the chemical. The drainage characteristics also change as sand accumulates in the voids and plugs them.
Source: AC 150/5200-30D, ¶4.71
That tells us grooving works. But how well?
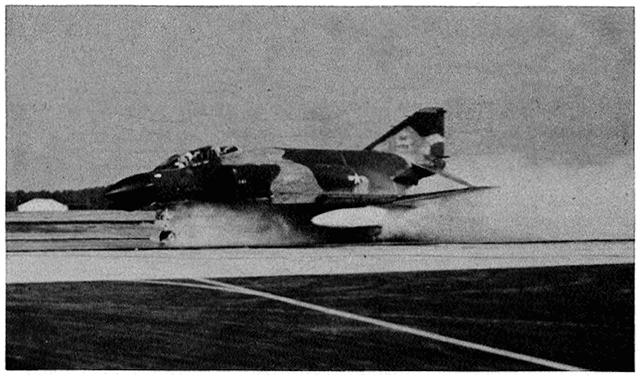
Test aircraft, from Pavement Grooving and Traction Studies, page 121, figure 2.
2
Why use runway grooves?
- Runway grooving is not used to provide drainage of water from the pavement surface. Drainage is provided by the transverse slope of the pavement. Grooves are cut in the runway surface transversely to the pavement centerline and make a secondary contribution to drainage.
- Runway grooving is not used to provide an increase in the friction capability of the pavement surface, which is provided by the quality of the microtexture / macrotexture combination of the pavement.
- Runway grooving provides forced water escape from the pavement surface under aircraft tires traveling at high speeds.
- Runway grooving does not eliminate hydroplaning, but it does reduce it to a manageable level.
- Runway grooving provides a higher degree of contact between aircraft tires and the pavement surface under the condition of standing water.
Source: Daiutolo
3
NASA Wallops Station tests
The NASA Langley Research Center conducted tests to determine the affects of grooved runways on aircraft braking performance at the NASA Wallops Station in 1968. Flight tests were conducted using an Air Force F-4D aircraft and a NASA Convair 990 aircraft. The results were presented in a conference report that compiled 27 papers from this and other studies. It is dry and convoluted writing, 521 pages of it, but there is a lot to be gained from selective reading. A copy of the report is linked, and excepts follow.
These tests were conducted in 1967. The FAA updated these tests in 1983, which fine tuned and corroborated the earlier findings. You can read about these tests in a presentation made in 2011: Daiutolo, which you can download below.
While the study covered various topics, such as tire wear and runway drainage, only three of its focus areas are of interest to us here:
- Grooved runway impact on tire rolling resistance.
- Grooved runway impact on tire cornering ability.
- Grooved runway impact on stopping capability.
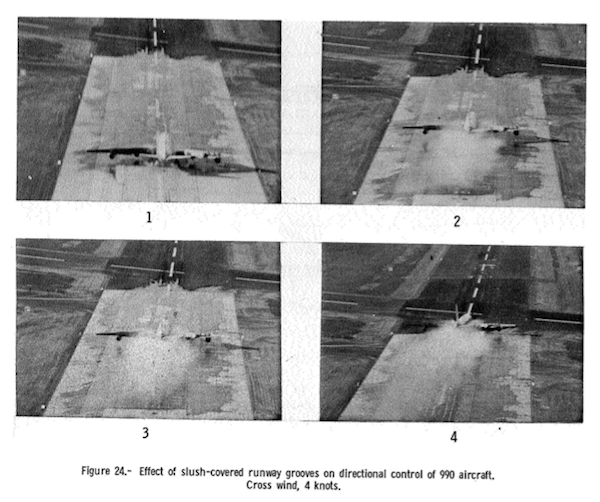
Effect of slush covered runway grooves on directional control of 990 aircraft, from Pavement Grooving and Traction Studies, page 63, figure 24.
Test set up
- [pg. 35] The purpose of the evaluation at the track was to determine which groove configuration, out of 19 configurations tested, offered the best aircraft tire braking capability; on the basis of these test results, the 1-in. x ¼-in x ¼-in. groove configuration was selected.
- [pg. 35] Runway 4/22 at NASA Wallops Station was selected, with test surface modification work (including installation of selected groove configuration) being completed in late 1967. Full-scale aircraft tests to determine the effects of grooved runway surfaces on aircraft landing and take-off operations under dry, wet, flooded, and slush-covered conditions were started February 1968.
- [pg 40] Nearly 200 test runs with an F-4D jet fighter and the 990 4-engine jet transport have been made on the landing research runway at NASA Wallops Station. With the data obtained from these two fully instrumented test aircraft, several factors affecting aircraft ground performance were evaluated.
Aircraft tire rolling resistance
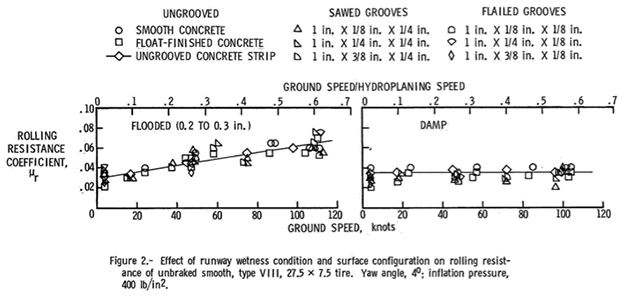
Effect of runway wetness condition and surface configuration, from Pavement Grooving and Traction Studies, page 49, figure 2.
- [pg. 37] With the pavement surface under flooded conditions (water depth varied from 0.2 to 0.3 in.), the rolling resistance coefficient of the smooth 27.5 x 7.5 test tire increases with speed but the data indicate no significant difference in the values obtained on the ungrooved concrete and those obtained on the other test surfaces. For damp conditions with no standing water on the surfaces, the rolling resistance values obtained on the ungrooved surface remain constant between 0.03 and 0.04 with increasing forward velocity.
- [pg. 38] The results of these unbraked tired tests indicate that transversely grooved pavement surfaces do not significantly affect tire rolling resistance.
Aircraft tire cornering ability
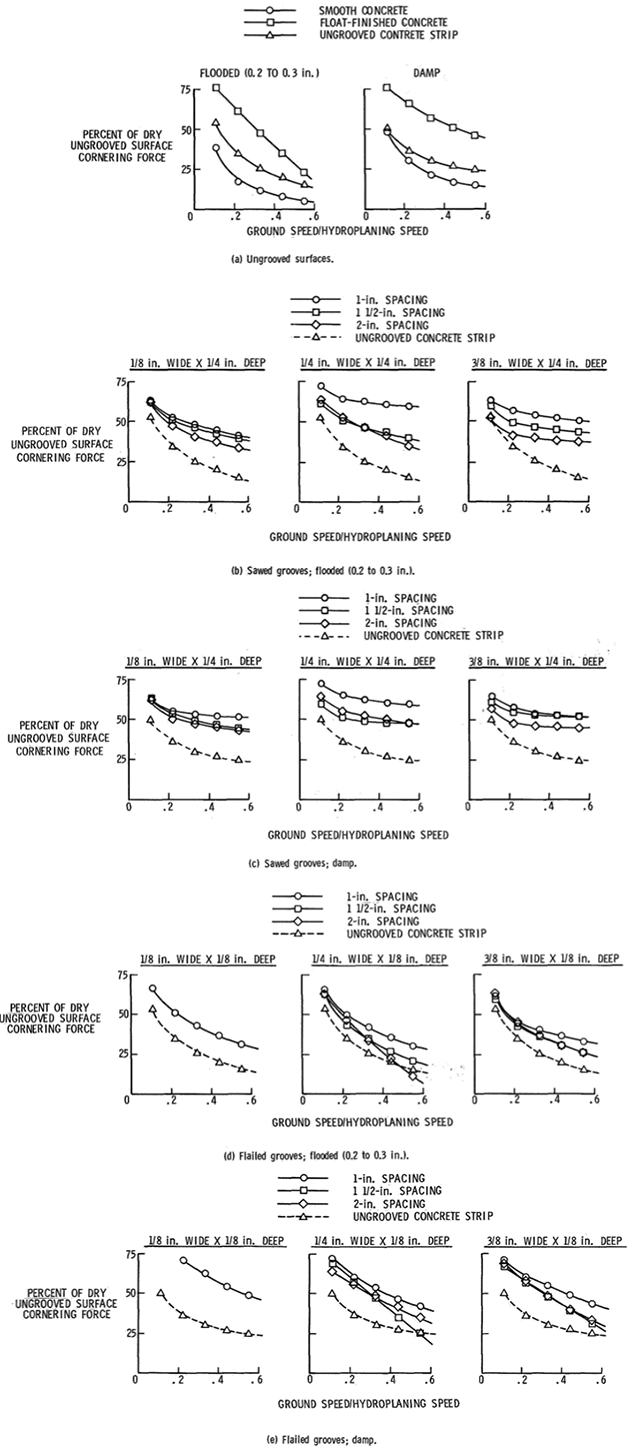
Cornering force, from Pavement Grooving and Traction Studies, pages 50 - 53, figure 3.
- [pg. 38] In this figure the cornering force obtained for each particular surface configuration is divided by the cornering force value obtained under the same conditions on the dry ungrooved surface. This value is then multiplied by 100 to express it as a percentage of dry ungrooved cornering force.
- [pg. 38] In general, the data show that a greater percent of the dry ungrooved surface cornering force was obtained on the damp test surfaces as compared to that obtained for flooded conditions. For similar wetness conditions, the data obtained on the ungrooved test surfaces are significantly lower than the data obtained on the sawed-groove and flailed-groove test surfaces. However, the degradation in tire cornering force developed on the saw-groove test surfaces for flooded conditions is substantially less than that from the damp surface condition, particularly at the higher, more critical speeds.
- [pg. 38] The data in [the figure] show that under flooded conditions the sawed groove configuration of 1 in. x ¼ in. x ¼ in. maintained the greatest percent of dry ungrooved surface cornering force throughout the test speed range.
A grooved runway gives you a definite advantage on takeoff in either the stop or go scenario. If the takeoff is continued, this so-called cornering ability helps keep you within centerline tolerances.
More about this: VMCG - Minimum Control Speed Ground.
Aircraft tire braking effectiveness
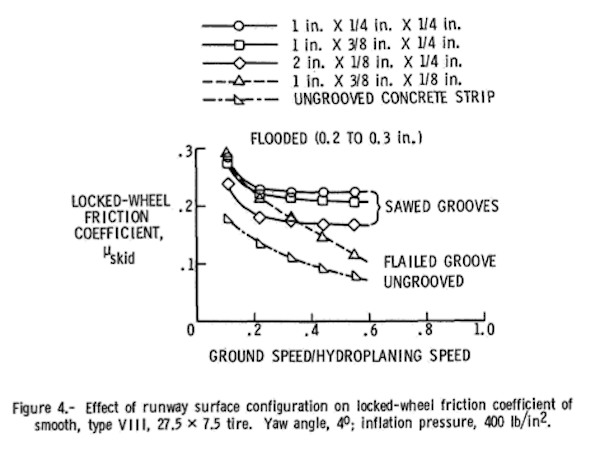
Braking effectiveness, from Pavement Grooving and Traction Studies, page 52, figure 4.
[pg. 39] In general, the locked-wheel friction coefficient data obtained on both the sawed- and flailed-groove surfaces are significantly higher than the data obtained on the ungrooved concrete test surface throughout the test speed range. However, as speed is increased, there is a rapid reduction in the locked-wheel friction coefficient obtained on the ungrooved and flailed groove test surfaces.
Braking Distances
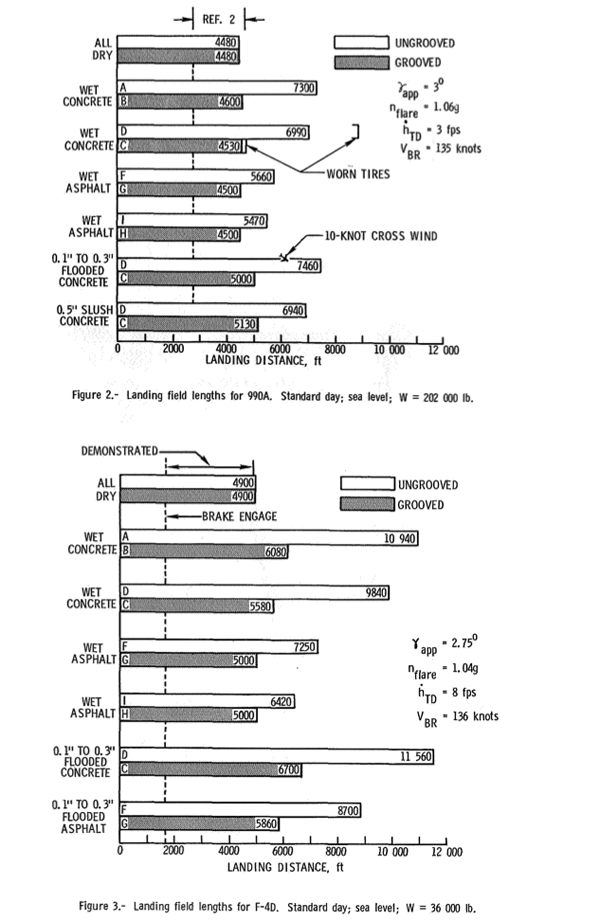
Landing field lengths, from Pavement Grooving and Traction Studies, pages 109 and 110, figures 2 and 3.
- [pg. 107] The present study of the effects of transverse runway grooving for the 990A and F-4D airplanes with regard to adverse-weather landing field lengths and balance take-off field lengths indicates the following conclusions:
- Transverse runway grooving effectively reduces landing field lengths under adverse weather conditions for a variety of runway surfaces.
- Essentially dry balanced field take-off performance is attainable for grooved runway surfaces in a wet and puddled condition, since grooving increases the critical engine-failure speed to practically dry-surface values.
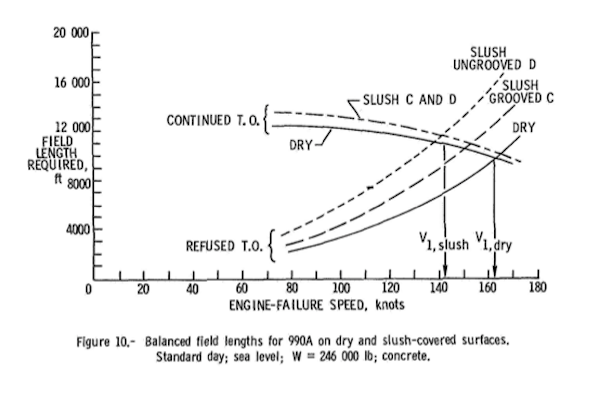
Balanced field lengths on slush, from Pavement Grooving and Traction Studies, page 113, figure 10.
- Only slight reductions in balanced field lengths are provided by grooving for take-off from slush-covered runways.
4
Regulatory
Certification
The Feds give you the option of factoring in grooved runways, but not all manufacturers do. In fact, some manufacturers have different rules for different aircraft.
The takeoff data must be based on . . . At the option of the applicant, grooved or porous friction course wet, hard-surfaced runways.
Source: 14 CFR 25 §25.105(c)(1)(ii)
Accelerate-stop distance. . . . At the option of the applicant, a higher wet runway braking coefficient of friction may be used for runway surfaces that have been grooved or treated with a porous friction course material.
Source: 14 CFR 25 §25.109(d)
Additionally, at the option of the applicant, wet runway takeoff distances may be established for runway surfaces that have been grooved or treated with a porous friction course, and may be approved for use on runways where such surfaces have been designed constructed, and maintained in a manner acceptable to the Administrator.
Source: 14 CFR 25 §25.1533(3)
No person may operate a turbine-engine-powered transport category airplane certificated after September 30, 1958, contrary to the Airplane Flight Manual, or take off that airplane unless— [ . . . ] (3) The takeoff weight does not exceed the weight shown in the Airplane Flight Manual to correspond with the minimum distances required for takeoff, considering the elevation of the airport, the runway to be used, the effective runway gradient, the ambient temperature and wind component at the time of takeoff, and, if operating limitations exist for the minimum distances required for takeoff from wet runways, the runway surface condition (dry or wet). Wet runway distances associated with grooved or porous friction course runways, if provided in the Airplane Flight Manual, may be used only for runways that are grooved or treated with a porous friction course (PFC) overlay, and that the operator determines are designed, constructed, and maintained in a manner acceptable to the Administrator.
Source: 14 CFR 91 §91.605(b)
In determining maximum weights, minimum distances, and flight paths under paragraphs (a) through (d) of this section, correction must be made for the runway to be used, the elevation of the airport, the effective runway gradient, the ambient temperature and wind component at the time of takeoff, and, if operating limitations exist for the minimum distances required for takeoff from wet runways, the runway surface condition (dry or wet). Wet runway distances associated with grooved or porous friction course runways, if provided in the Airplane Flight Manual, may be used only for runways that are grooved or treated with a porous friction course (PFC) overlay, and that the operator determines are designed, constructed, and maintained in a manner acceptable to the Administrator.
Source: 14 CFR 121 §121.189(e)
In determining maximum weights, minimum distances, and flight paths under paragraphs (a) through (d) of this section, correction must be made for the runway to be used, the elevation of the airport, the effective runway gradient, the ambient temperature and wind component at the time of takeoff, and, if operating limitations exist for the minimum distances required for takeoff from wet runways, the runway surface condition (dry or wet). Wet runway distances associated with grooved or porous friction course runways, if provided in the Airplane Flight Manual, may be used only for runways that are grooved or treated with a porous friction course (PFC) overlay, and that the operator determines are designed, constructed, and maintained in a manner acceptable to the Administrator.
Source: 14 CFR 135 §135.379(e)
FAA Safety Alert for Operators (SAFO)
- Landing overruns that occur on wet runways typically involve multiple contributing factors such as long touchdown, improper use of deceleration devices, tailwind and less available friction than expected. Several recent runway-landing incidents/accidents have raised concerns with wet runway stopping performance assumptions. Analysis of the stopping data from these incidents/accidents indicates the braking coefficient of friction in each case was significantly lower than expected for a wet runway as defined by Title 14 of the Code of Federal Regulations (14 CFR) part 25 § Section 25.109 and Advisory Circular (AC) 25-7D methods.
Source: SAFO 19003
The FAA has had a change of heart about how we deal with wet runways. It used to be they said add 15% and good luck. A preponderance of evidence over the years indicates 15% is not enough.
- These incidents/accidents occurred on both grooved and un-grooved runways. The data indicates that applying a 15% safety margin to wet runway time-of-arrival advisory data, as recommended by SAFO 19001 (or current guidance), may be inadequate in certain wet runway conditions. Takeoff and Landing Performance Assessment (TALPA) procedures implemented by the FAA on October 1, 2016, added new insight as to how flightcrews can evaluate runway braking performance prior to landing. TALPA defines WET as “Includes damp and 1/8-inch depth or less of water,” while CONTAMINATED is “greater than 1/8-inch of water.”
Source: SAFO 19003
Test data has shown that thin coatings of water on a smooth runway can greatly impact stopping distances, but if the surface is grooved, the runways are almost as good as dry if the coating is thin. That same test data shows that when the thickness of the water increases, the benefit of a grooved runway quickly disappears.
- These overruns have occurred on grooved and smooth runways during periods of moderate to heavy rain. Analysis of these incidents/accidents indicates that the braking coefficient of friction in each case was significantly lower than expected, and that 30 to 40 percent of additional stopping distance may be required if the runway transitions from wet to contaminated based on the rainfall intensity or reported water contamination (greater than 1/8-inch depth). For the operational in-flight landing assessment, determining whether the runway is wet or potentially contaminated is the pilot’s responsibility.
- The TALPA RCAM recommends using landing performance data associated with medium to poor braking or RwyCC of 2, if greater than 1/8-inch of water is anticipated to be on the runway. When planning to land on a smooth runway under conditions of moderate or heavy rain, or when landing on a grooved or PFC runway under heavy rain, pilots should consider that the surface may be contaminated with water at depth greater than 1/8 inch and adjust their landing distance assessment accordingly.
Source: SAFO 19003
An RCAM Runway Condition Code of 2 can be thought of as "Medium to Poor."
- Knowing ahead of time whether your aircraft can or cannot stop within the Landing Distance Available if runway conditions deteriorate to a medium to poor condition (RwyCC = 2) is critical when operating in moderate or heavy rain. Go-around, holding, or diversion may be necessary if rainfall intensity increases beyond what might be acceptable for the intended operation.
Source: SAFO 19003
How does one know ahead of time whether or not their airplane can stop with a medium to poor runway condition? This depends a lot on where the report is coming from. See: Contaminated Runways.
For more about this, see: Runway Condition Codes.
Gulfstream Example
I've flown aircraft that allowed pilots to consider wet grooved runways to be essentially dry. The Gulfstream G450 does not. The performance section of that AFM does not mention runway grooves at all. The only thing in our books on the subject appears in G450-OIS-02:
For landing operations on a wet, grooved runway, data in this OIS will be conservative.
Source: G450-OIS-02, page 19
This leads me to believe Gulfstream has not factored in grooved runways and wants you to use it as a safety pad. Interestingly, the rules for the G150 do allow the consideration of grooved runways.
More about this: Braking Action.
References
(Source material)
14 CFR 25, Title 14: Aeronautics and Space, Airworthiness Standards: Transport Category Airplanes, Federal Aviation Administration, Department of Transportation
Advisory Circular 150/5200-30D, Airport Field Condition Assessments and Winter Operations Safety, 3/8/2017, U.S. Department of Transportation
Daiutolo, Hector, The Benefit of Runway Grooving, FAA/Asphalt Institute Airport Pavement Workshop, October 18-20, 2011.
Gulfstream G450 Operational Information Supplement, G450-OIS-02, Contaminated Runway Performance, Revision 1, August 3, 2011
NASA SP-5073, Pavement Grooving and Traction Studies, 1969
Safety Alert for Operators, SAFO 19003, Turbojet Braking Performance on Wet Runways, 7/2/19, U.S. Department of Transportation
Please note: Gulfstream Aerospace Corporation has no affiliation or connection whatsoever with this website, and Gulfstream does not review, endorse, or approve any of the content included on the site. As a result, Gulfstream is not responsible or liable for your use of any materials or information obtained from this site.